Combining different methods of artificial intelligence
C3 AI combines several of the latest theoretical methods from research and science, such as machine learning, and uses them to generate various planning scenarios for the user, e.g. minimizing delivery delays or maximizing plant utilization.
Dynamic global planning: on-time delivery and setup time savings
The result is automatically generated job schedules that are optimized considering delivery dates, material availability and replenishment times, setup time savings and available capacities. New jobs can be scheduled dynamically at any time. Flexible machine configurations allow you to optimize all setup time-relevant factors. This means that you will only need to set up your machines when absolutely necessary. With flexible weightings, you can place more emphasis on current market demands, such as on-time delivery of orders from key accounts or minimum costs.
The figure on the right shows that the green line is more oriented towards meeting delivery dates and throughput times, in contrast to the blue line, where the emphasis is more on capacity utilization and setup time savings. Red, on the other hand, is a mix in which all factors are roughly equally weighted.
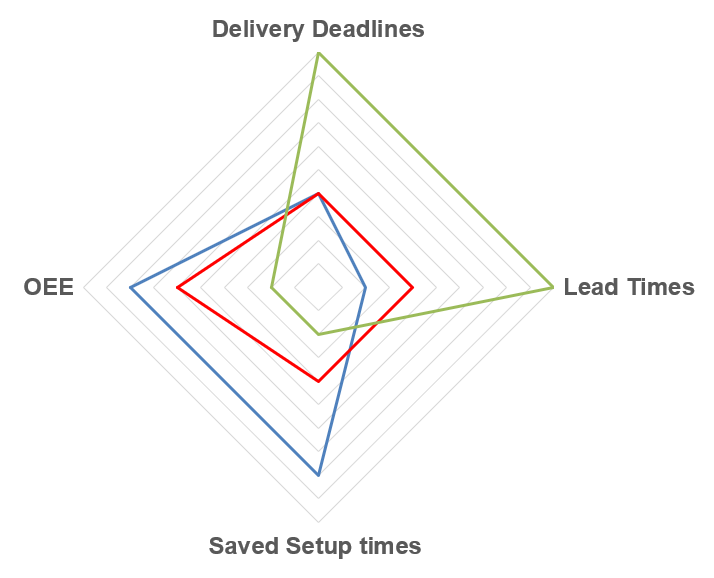
Fully automated production planning
Every production process has different goals that need to be achieved. These optimization goals include:
- Minimization of missed delivery dates
- Minimization of set-up times
- Maximization of overall equipment effectiveness (OEE)
- Lead time
- Total late days
C3 AI helps you to optimize towards these goals. The following aspects are taken into account, too:
- Capacities and material availability
- Fixed dates and idle times
- Frozen zone
- Alternative resources
All objectives are taken into account with weightings that you determine in advance. In this way, the AI finds the optimum solution for your needs.
Minimization of setup times
By default, the AI has the setup-relevant properties of a job for a specific machine. For example, for machine A, the job’s material is setup-relevant, and for machine B, the job’s coating and tool 1 are setup-relevant. The AI then tries to arrange the jobs for each machine in a way that minimizes the number of setups, taking into account the other planning goals. For example, a setup savings in minutes is specified if two jobs with the same material are run back-to-back on machine A. The set of rules can be fine-tuned to a very high degree.

Setup optimization of the order sequence for multiple jobs
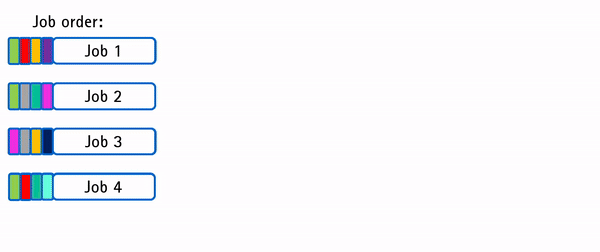
Live key performance indicators and statistics
Live statistics show the current KPIs such as setup time saved, number of delayed jobs, total late time, overall equipment efficiency, or whatever key factors you want to see. It’s your choice!
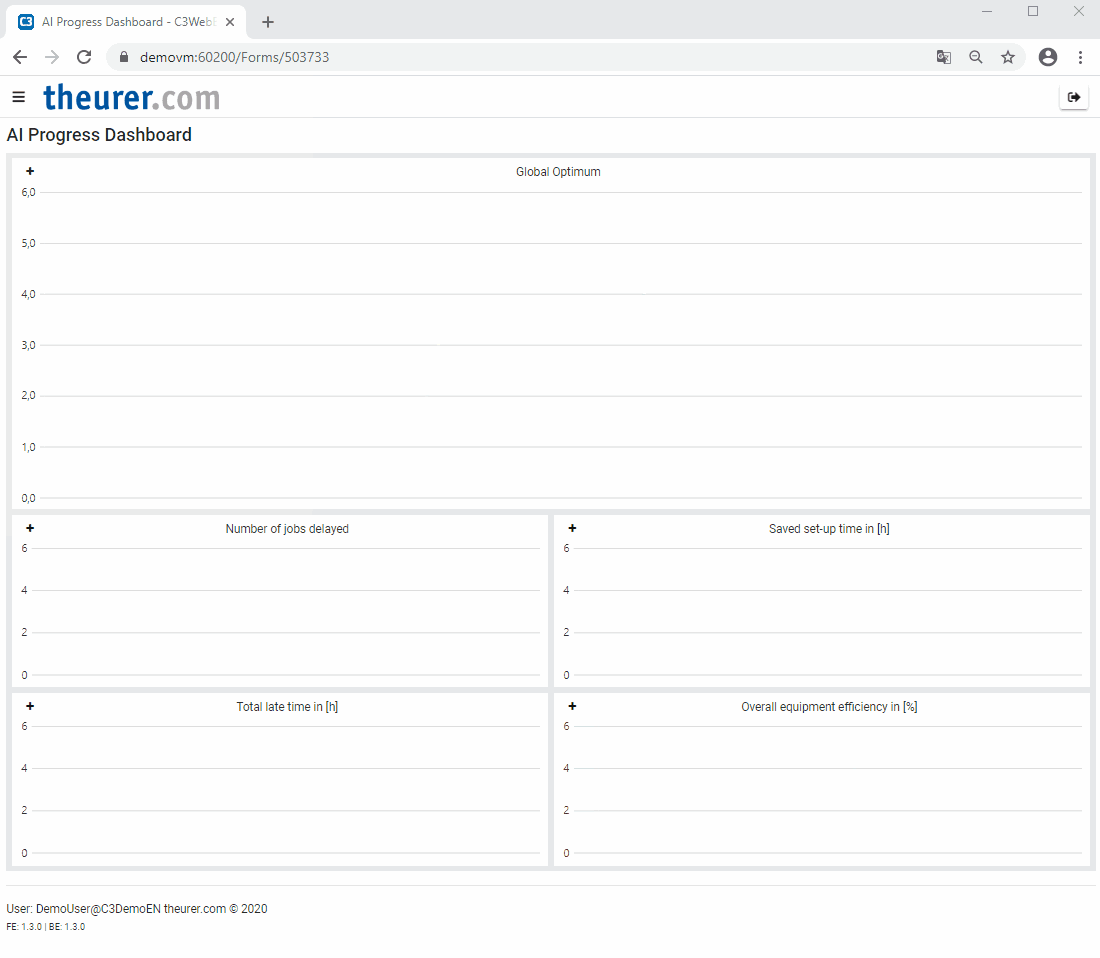
By the way: The enormous computing power for this AI application is provided by theurer.com in high-performance data centers via the cloud. The more time the AI is given, the better the results. Typically, an optimum is reached after one to two minutes.
Cloud Integration
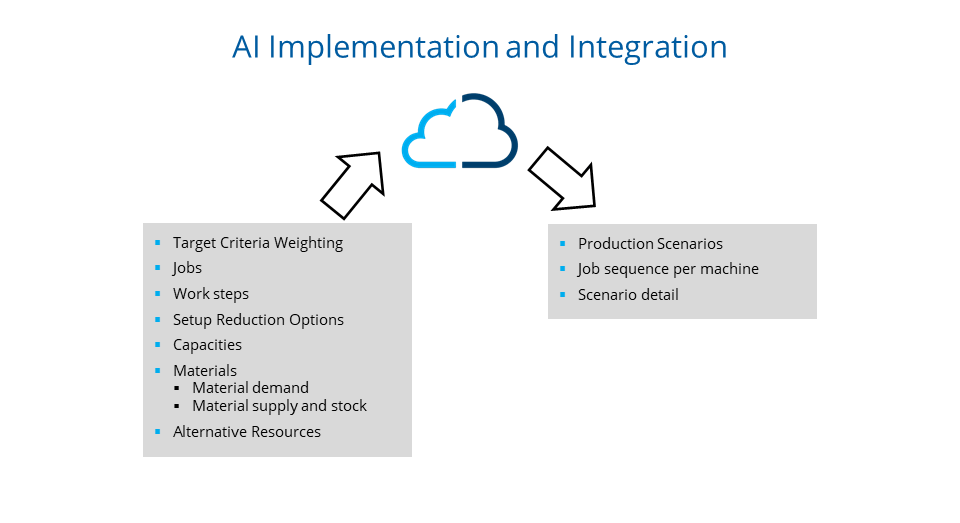
The AI engine runs in the cloud and is controlled via REST API.
Basically, you enter a job list with job characteristics and deadlines, work steps with time and material consumption, and a shift calendar for resources.
Result
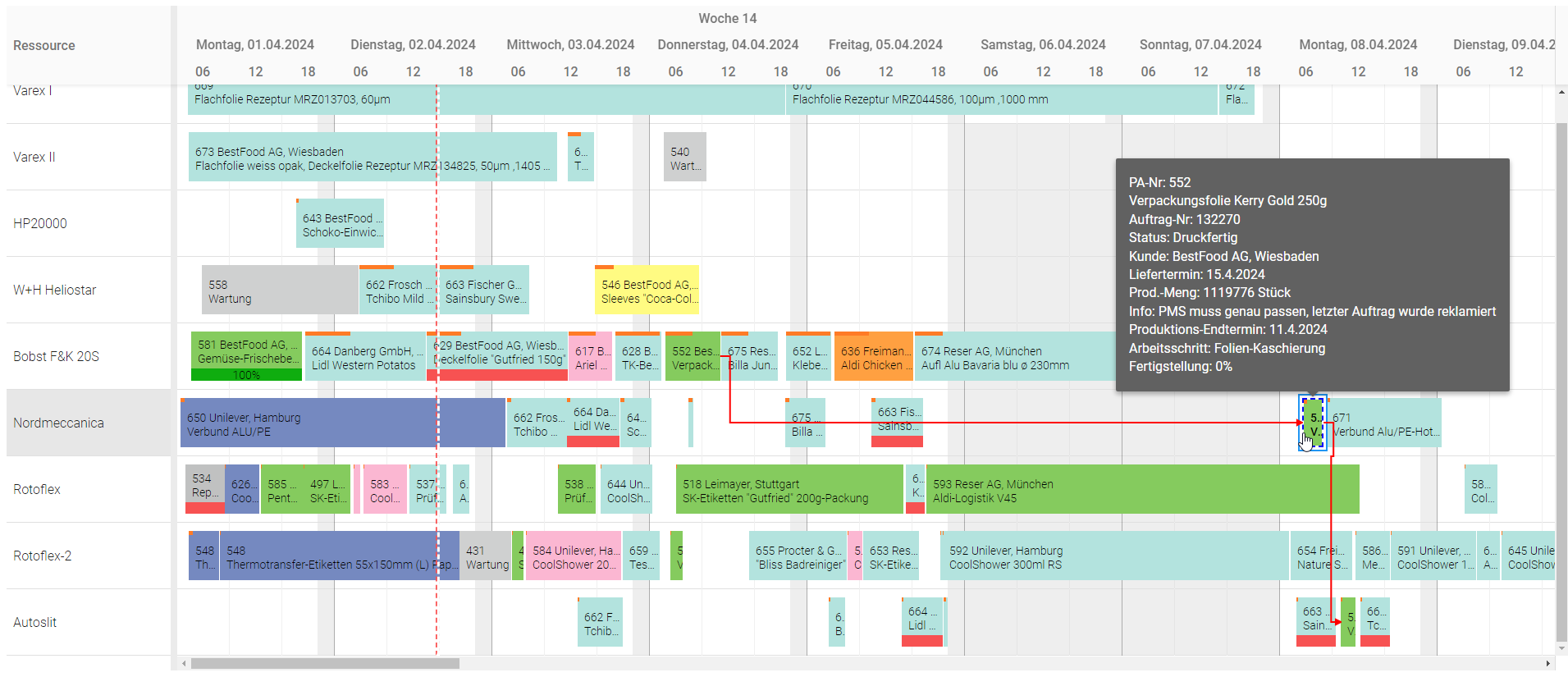
Standalone cloud service and integration REST API
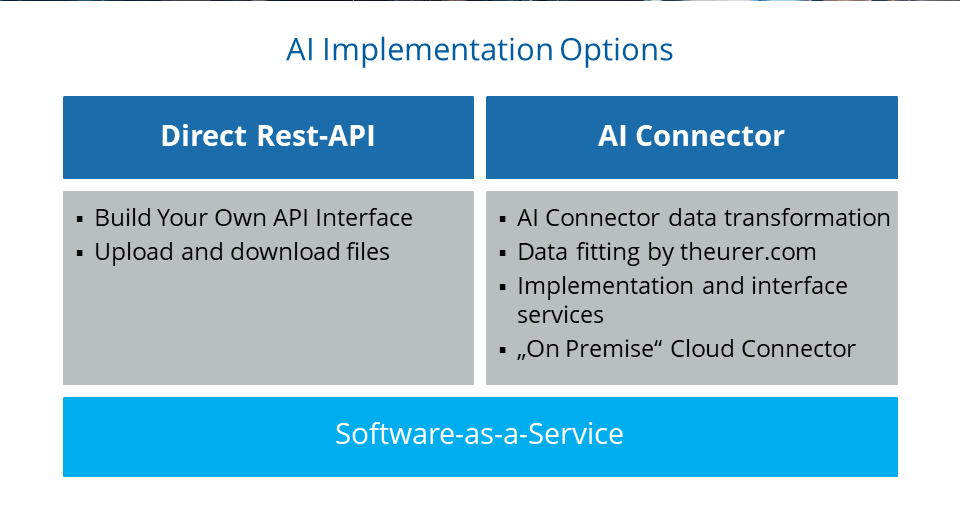
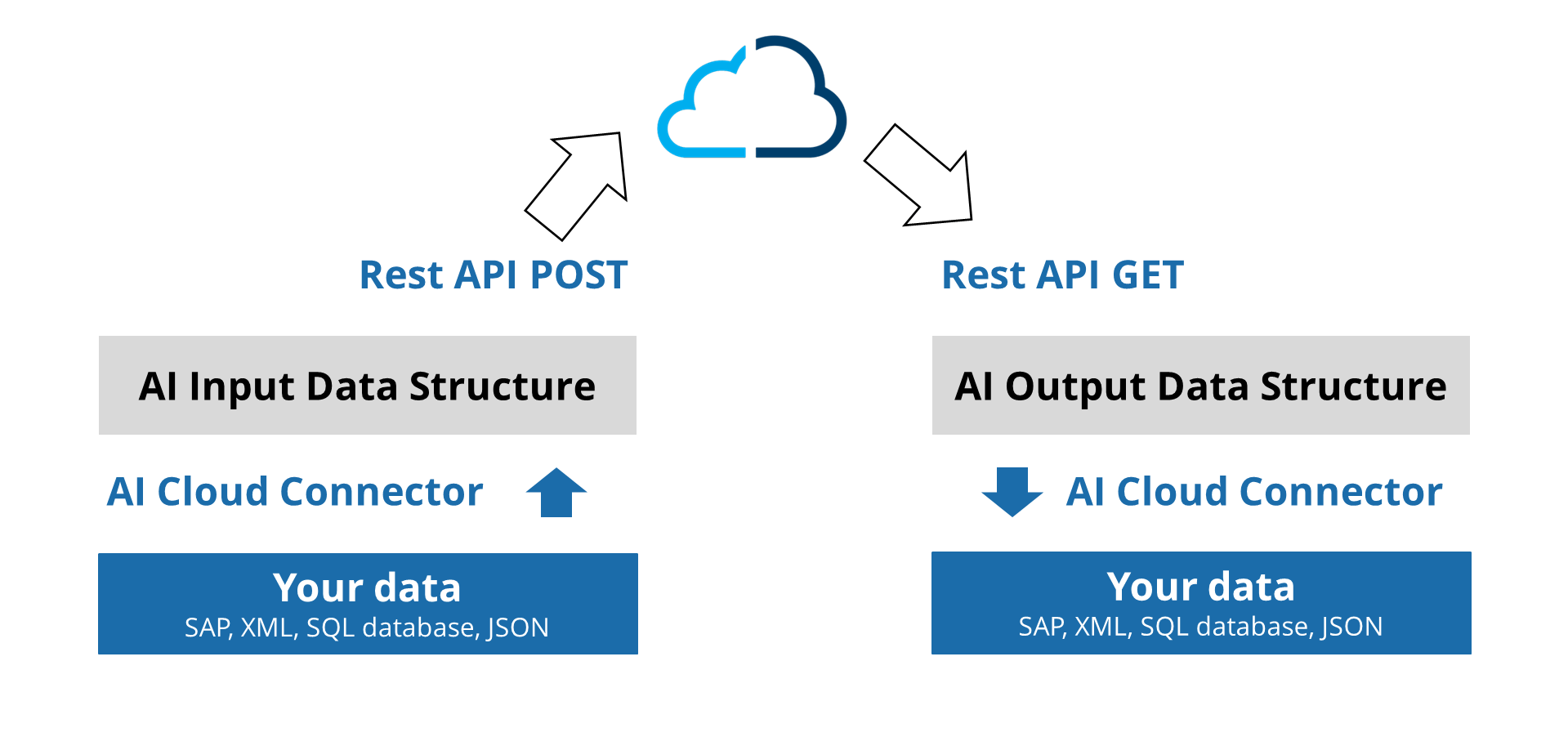
The AI engine runs in the cloud and is accessed via a Rest API.
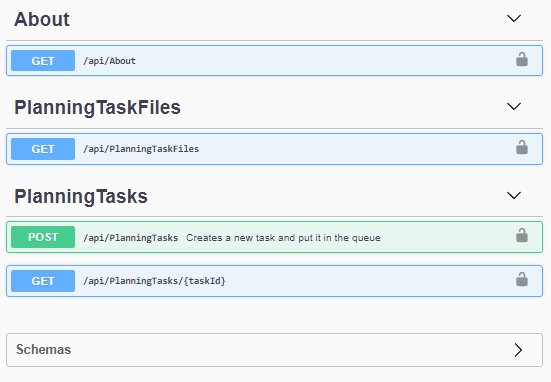